优化
酵母菌发酵罐的发酵过程与产量需从
菌种特性、培养基配方、发酵条件控制、设备设计及过程监控等多维度协同改进,通过系统性策略提升生物量积累、代谢效率及产物得率。以下是具体优化方向与措施:
一、菌种选育与改良:强化代谢能力
1. 高活性菌株筛选
通过自然分离或诱变育种(如紫外线、化学诱变剂)筛选具有高生长速率、高糖利用效率及抗逆性强的酵母菌株(如酿酒酵母Saccharomyces cerevisiae工业菌株)。例如,筛选能在高糖浓度(如30% w/v)下保持高活性的菌株,避免渗透压抑制导致的生长停滞。
2. 基因工程改造
利用CRISPR-Cas9等技术敲除副产物合成基因(如甘油合成途径的GPD1/GPD2基因),减少碳源分流;或过表达关键代谢酶基因(如丙酮酸脱羧酶PDC、乙醇脱氢酶ADH),强化目标产物(如乙醇)合成路径。例如,工程菌可将乙醇产量提高10%~20%。
3. 适应性进化
在目标发酵条件下(如高温、高乙醇浓度)连续传代培养,筛选适应高压环境的菌株。例如,通过逐步提高乙醇浓度(从5%至12% v/v)驯化菌株,增强其对代谢抑制物的耐受性。
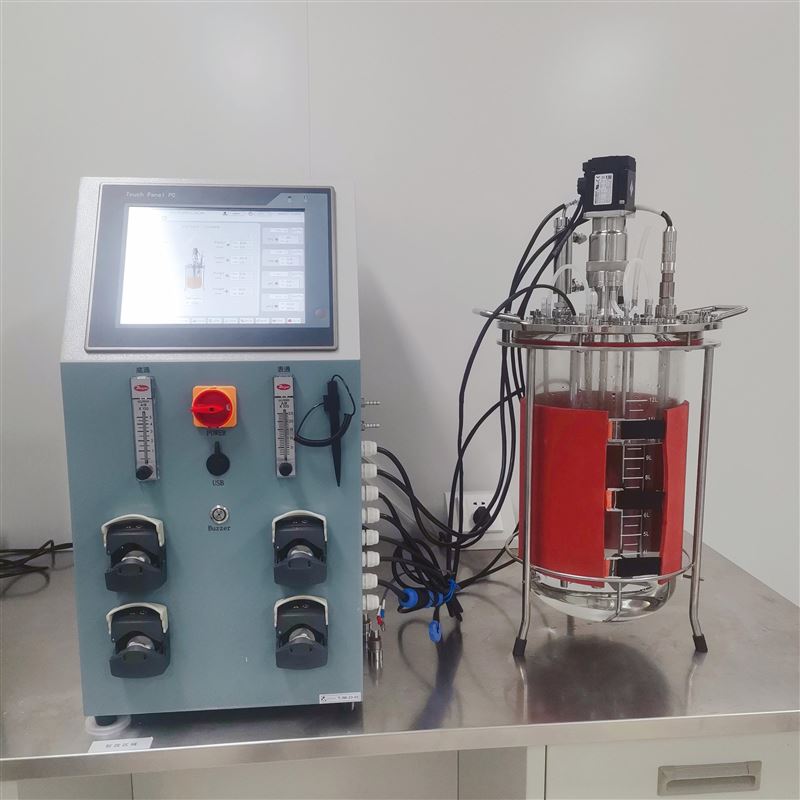
二、培养基优化:精准供给营养
1. 碳源选择与浓度调控
碳源类型:葡萄糖是最易利用的碳源,但高浓度会引发“葡萄糖效应”(抑制其他基因表达)。可部分替代为蔗糖、麦芽糖或木质纤维素水解液(如玉米秸秆水解糖),降低成本并延缓碳源消耗速率。
浓度控制:初始糖浓度需匹配菌株耐受能力(如酿酒酵母通常为15%~25% w/v),避免初始浓度过高导致渗透压抑制;采用补料分批培养(Fed-batch)动态补充碳源,维持糖浓度在1%~5% w/v,延长对数生长期。
2. 氮源优化
速效氮源(如酵母提取物、蛋白胨)促进菌体快速增殖;迟效氮源(如硫酸铵、尿素)维持稳定代谢。典型配比为速效:迟效=3:1~4:1。
氨离子浓度:过量铵盐(>100mmol/L)会抑制呼吸链酶活性,需通过pH反馈控制补料速率(如维持pH 4.5~5.5,间接调控氨离子供给)。
3. 微量营养素补充
添加维生素(如生物素、硫胺素)、矿物质(如磷酸盐、镁离子)及微量元素(如锌、铜),激活代谢关键酶(如乙酰辅酶A合成酶需生物素作为辅因子)。例如,添加0.01mg/L生物素可使乙醇产量提升8%~15%。
三、发酵条件精准控制:动态匹配代谢需求
1. 温度调控
对数生长期:维持较高温度(如30℃~32℃)加速细胞分裂;
产物合成期:适当降温(如28℃~30℃)减少呼吸消耗,促进产物积累。
动态控制:通过温度传感器实时反馈,结合菌体生长速率(OD600)调整温度,避免高温导致酶失活或低温抑制代谢。
2. pH管理
初始pH:设定为4.0~5.5(酵母最适范围),避免酸性过强抑制菌体生长或碱性过强导致氨挥发。
动态调节:通过自动流加酸(如H₂SO₄)或碱(如NaOH)维持pH稳定,或利用代谢副产物(如CO₂溶解产生碳酸)自然调节pH。例如,乙醇发酵中pH降至3.5以下会抑制PDC活性,需及时补碱。
3. 溶氧控制
有氧阶段(菌体增殖期):维持高溶氧(DO>20%饱和度),促进细胞呼吸与生物量积累;
厌氧阶段(产物合成期):降低溶氧(DO<5%饱和度),诱导厌氧代谢途径(如乙醇发酵)。
动态调节:通过搅拌转速(200~800rpm)与通气量(0.5~2.0vvm)协同控制DO,避免泡沫过多(添加消泡剂如硅油)或溶氧不足(导致代谢转向副产物合成)。
四、发酵设备优化:提升传质与混合效率
1. 搅拌与通气系统改进
搅拌桨设计:采用高效轴向流搅拌桨(如Rushton涡轮桨+平直叶组合),增强气液混合与溶氧传递效率;
通气策略:微孔曝气(气泡直径<1mm)可提高氧传递系数(kLa),降低能耗;
消泡装置:机械消泡桨与化学消泡剂(如聚二甲基硅氧烷)结合,避免泡沫溢罐导致染菌或产物损失。
2. 罐体结构优化
高径比(H/D):增大H/D(如3:1~4:1)可提升溶氧分布均匀性,减少局部缺氧;
夹套与冷却系统:强化传热能力(如双层夹套+螺旋导流板),快速移除发酵热(每克葡萄糖发酵产热约20kJ),避免温度波动>±1℃。
五、过程监控与智能调控:数据驱动优化
1. 在线监测技术
生物量检测:在线OD传感器(如红外光谱法)实时监测菌体浓度,避免取样滞后;
代谢物分析:在线HPLC或近红外光谱(NIR)监测糖浓度、乙醇及副产物(如甘油、有机酸)含量,动态调整补料速率;
环境参数:pH、DO、温度、溶氧传感器集成至DCS系统,实现多参数联动控制。
2. 模型预测控制(MPC)
基于代谢动力学模型(如Monod方程、Gompertz方程)预测菌体生长与产物合成趋势,提前调整补料、通气及温度参数。例如,通过模型预测糖耗速率,在糖浓度降至1% w/v前启动补料,维持高代谢活性。
六、下游分离与产物回收:减少损失
1. 发酵液预处理
固液分离:采用离心(8000~12000rpm)或膜过滤(0.2~0.45μm微滤)去除菌体,避免产物被细胞吸附;
副产物去除:通过离子交换树脂吸附有机酸(如乳酸),减少对产物纯度的影响。
2. 产物高效提取
乙醇回收:采用多级蒸馏(如三塔差压蒸馏)或渗透汽化膜技术,降低能耗(传统蒸馏能耗约30MJ/t乙醇,渗透汽化可降至15MJ/t);
其他产物:如酵母蛋白可通过喷雾干燥直接制成饲料添加剂,提高资源利用率。
七、典型案例:乙醇发酵优化效果
初始条件:初始糖浓度20% w/v,温度30℃,pH 5.0,DO 20%饱和度;
优化后:
采用补料分批培养(初始糖浓度10%,补料速率0.2g/(L·h)),糖利用率从85%提升至95%;
动态控制pH(4.5~5.5)与溶氧(对数期DO>20%,产物期DO<5%),乙醇产量从85g/L提高至105g/L(增幅23.5%);
引入基因工程菌(敲除GPD1基因),甘油产量降低40%,乙醇得率提高15%。
总结
酵母菌发酵过程的优化需以菌种为核心,通过培养基精准供给、环境条件动态匹配及设备性能提升,构建高效代谢网络;结合在线监测与智能调控技术,实现从“经验驱动”到“数据驱动”的转变。最终目标是在降低生产成本的同时,显著提升生物量、产物浓度及产率,满足工业化规模生产需求。